
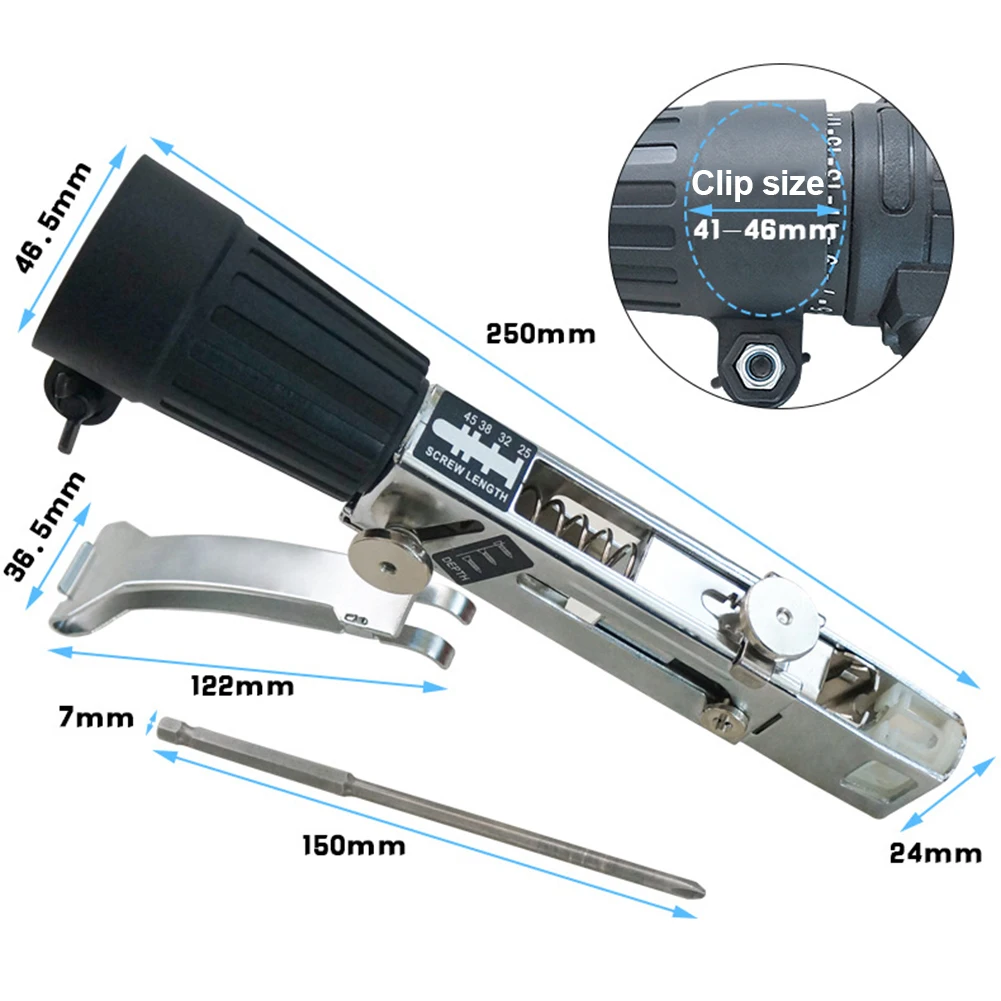
For my job i run the spindle at 3600 rpm, the oil at 1000 psi and run the feed at about 1.25 in/min. You need to have as was stated a bushing that gets the drill started dead on and special cutting oil fed to the gun drill under pressure. 262 diameter in 41L40 in about 12 minutes without stopping. i built my own deep hole drill set up on an old lathe bed. Gun drilling is pretty easy if you have the proper set up. Here is a link to Drillmaster/Eldorado's website, read it through but the bottom seems to have some good info.įound some tungaloy information that is decent, it is in metric.
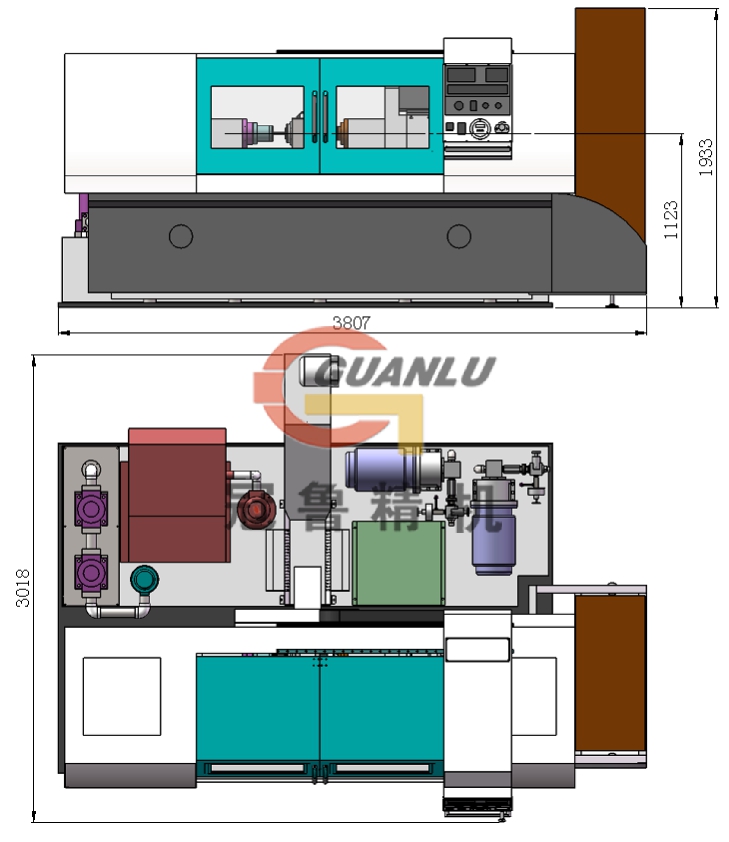
Maybe someone has more or better experience, hope this helps. We got good money for the job so there was little fretting over buying new ones to make it easier, helps that the material was expensive too. We tried regrinding them and sending them out for regrinding but got inconsistent results so we ended up just purchasing new ones. We had pretty good experience with them, we replaced them every 50 pieces, so like 300 inches. I was able to get a book from them that had speeds and feeds for the gun drill I had when i was looking at gun drills. I think hard materials chip nice and work great with these. Coolant was at the top end for better lubricity. I think I remember our speed being 220 sfm and feed of 0.001'-0.0012'/rev if I remember correctly, at the end you stop the spindle and pull it out. Then you put the drill in at stop spindle at like double the diameter, turn the spindle on, turn the coolant on and drill. A very important thing is the pilot drill, which needs to be like 0.001' bigger and like an 0.75-1' deep. I used a Drillmasters gun drill it was in a lathe. The International Journal of Advanced Manufacturing Technology Springer Journals I haven't done gun drilling in like 10 years, I did a bunch in Astralloy. Considering the force system and the gun drilling performance, the optimized cutting parameters could be chosen basically. Thus, the fluctuations of hole cylindrical decreased with the increasing of cutting speed. The high cutting feed associated with the high cutting force generated the large beating and lower the hole cylindricity deviation. The hole machining quality was highly dependent on the hole diameter and cylindricity. The chip length became short with the high cutting feed and the low cutting speed. The wear mechanical was the combination of the adhesive wear, diffusion wear, oxidation wear, and breakage in the gun drill.
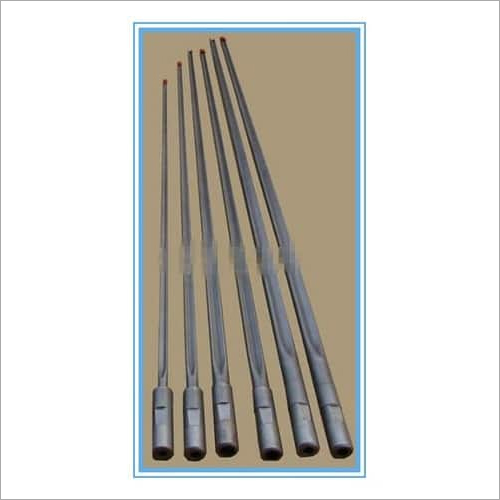
Both the calculated and experiment data revealed that the force and torque increased with the cutting feed ascending and the cutting speed descending. A carbide gun drill force system had been established by the integration of forces on the main cutting edge, wear pad and outer diameter (OD) relief, and the mechanical equilibrium equations, applying specific energy model, which consisted of the geometry parameters, machining parameters, and material properties. This paper focused on the force system and performance of the welding carbide gun drill to cut AISI 1045 steel. Wang, Yongguo Jia, Wenxing Zhang, Jingsong The force system and performance of the welding carbide gun drill to cut AISI 1045 steel The force system and performance of the welding carbide gun drill to cut AISI 1045 steel
